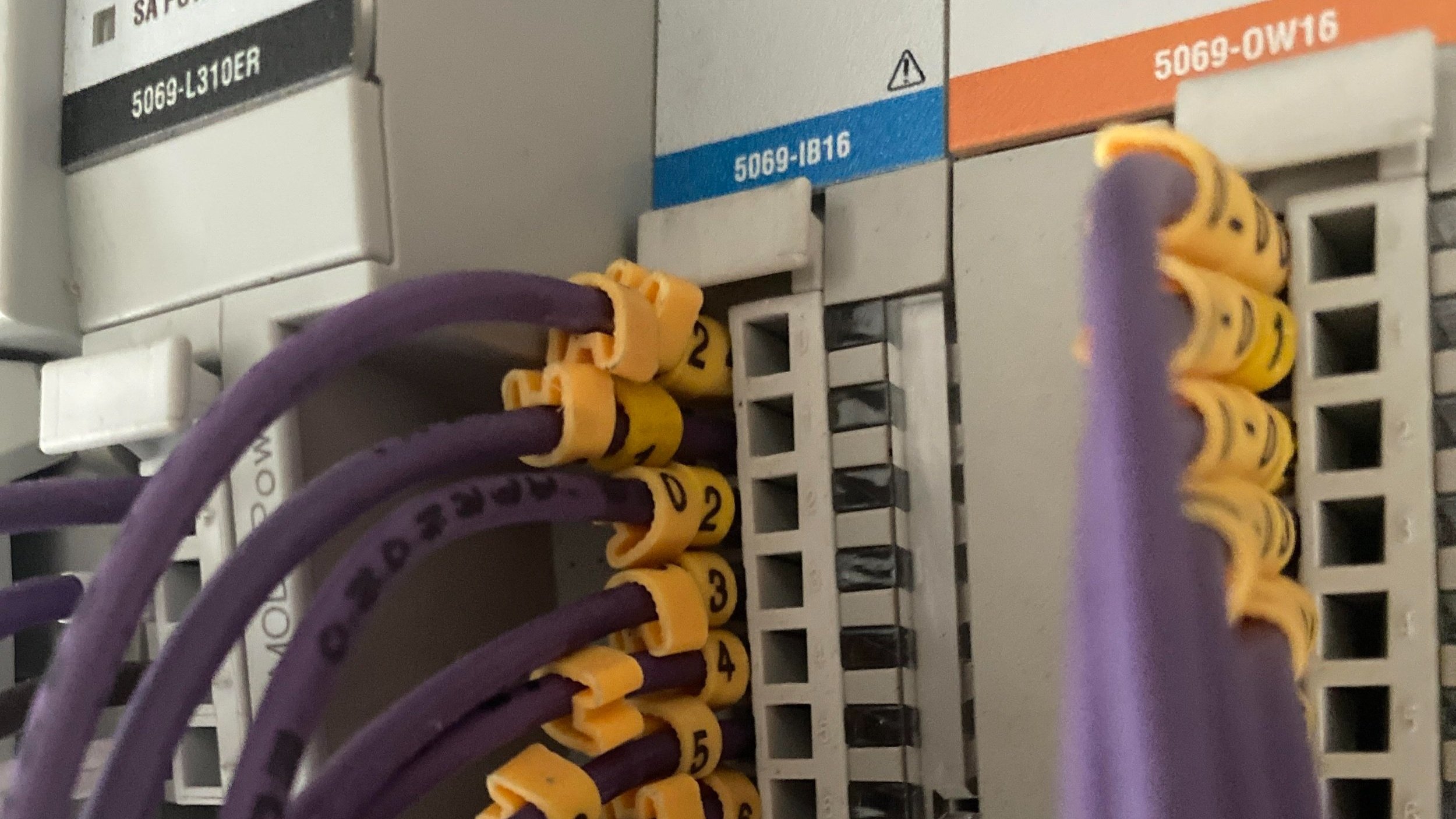
Case Studies
SCADA CONTROL SYSTEM
Project: SCADA Automation
Client: TransCIP - Australia
Our client developed and built a CIP plant in Melbourne. The CIP plant is designed to clean trucks used for carrying milk, cream and oil. The cleaning is done with caustic, acid, and a pre rinse agent.
Problem:
The challenge was to find a tailor-made SCADA automation software program that will deliver the recording and reporting requirements for this plant.
Data on similar CIP plants is manually recorded on a clip board, and there is a lot of data collected, which needs to be available for auditing later. Our client needed an SCADA control system with accurate reporting system that would satisfy auditing requirements.
The SCADA equipment must be able to produce reports on all the things that are usually recorded manually, including wash dates, carrier names, truck numbers, the time the wash takes, the chemical the wash used, the temperature of the chemical and how much chemical was used for each wash.
The SCADA control system must be able to push data to a web portal and receive data from the web portal. The SCADA software must also have an auto emailing function, print to a mobile printer and allow the client to have remote access to his plant
The SCADA software must supply a comprehensive alarm application with a pre-warning function.
The software must mimic graphics to assist with visual management.
What we did:
After comprehensive market research, our client could not find a SCADA control system off the shelf that could deliver this unique requirement. ACSE understands that no two requirements are the same - that is why we develop tailor-made SCADA software packages for our clients.
We delivered a SCADA automation package that not just met, but exceeded the client’s expectations.
Our SCADA equipment delivered all the stated requirements, plus it features a documented condition of events, informing the operator of any wrong selections, and helping the operator to choose the right sequence of events. This allows a layman to operate the plant without prior knowledge or training on the system.
The SCADA equipment was developed on a 21.5-inch touch screen. The software was developed with big interfacing buttons and large readable message fonts. Large popup message boxes help the operators operate the plant efficiently.
Outcome:
All information is collected, recorded and reported in a format that meets audit requirements.
The plant was built in Melbourne, we commissioned the project from our office in Manukau during the COVID lockdown. The project was delivered on time and within budget.
The SCADA automation system can be maintained and upgraded from New Zealand.
PLC UPGRADE
Project: PLC upgrade
Client: Godfrey Hirst
Our client has a PLC machine that measures the length of carpets and cuts the carpet into specific sizes for each order. The machine was fitted with an old Rockwell SLC PLC controller with variable drives that control the speed of the motors, communicating over “Data Highway Plus” protocol to the PLC.
Problem:
When one of these drives fails, the machine can be down for hours before it can be fixed and go back into production.
The PLC controller would sometimes lose the matrix that monitors the carpet size, when this happens, values have to be put back into the program manually.
The touch screen used by the operators to interface to the PLC machine was old and rundown, so it sometimes lost connection to the PLC. Every time this machine fails, the machines upstream feeding the carpet have to be stopped as well. Starting each machine back up can take up to 15 minutes.
Machine utilisation was severely impacted by these problems, resulting in slower throughput of orders, lost productivity and lost profits.
What we did:
We designed a new control system that communicates over Ethernet (a standard protocol for industrial machines).
We converted the existing Programmable Logic Controller program and upgraded it to be installed into the latest PLC controller. The variable drives were replaced with the latest drives and the communication between the drives and the PLC was upgraded to Ethernet. All the signal input and output cards were upgraded with new power supplies.
The old touch screen that the operator used to enter carpet cut sizes into the system was replaced with a new touch screen. The new touch screen interface to the PLC via Ethernet this makes the system more robust and reliable.
Machine sensors that were communicating over Data Highway Plus, has been upgraded to communicate direct to the new input and output cards on the Programmable Logic Controller.
We helped identify the vulnerability on products no longer being available on the market by Rockwell. A failure here had the potential for a catastrophic failure resulting in the main line being down for weeks. We helped engineer a suitable replacement with the most suitable part.
Outcome:
The new system eliminated the control system breakdowns.
After the PLC machine was brought up to standard, production could meet their throughput KPI’s.
The KPI’s were based on the best possible time it could have taken to run the given amount of good product. This assumes running at rated speed with no stoppages. Calculated as follows:
Good Product ÷ Rated Line Speed.
The client can now meet the market demand for carpet. Down time on the machine was reduced by 80 percent.
We also worked with the production manager to add additional automated controls such as automated lengths to reduce operator error by decrease wasted product and speeding up the process line.
FLOW METERING SYSTEM
Project: Flow metering system
Client: Ramspecs
Our client transfers milk from smaller tanker trucks (coming from the farm) into large multi-compartment tankers that transport milk to the factory. Some farms are over 200kms away from the factory, so it is better for smaller tankers to collect the milk from the farm and then transfer the milk into larger tankers for the journey to the factory for processing.
Problem:
The truck that picks the milk up from the farm only has one compartment of 30 000 litres, whereas the truck carrying the milk to the factory has five compartments of 15 000 litres inside the tank. The driver can only transfer the amount of milk that the compartment can hold. The driver needs to enter the exact amount of milk into the flow meter to control the transfer pump. If he pumps in too much milk the tank will overflow, if he pumps in too little milk the truck runs partly empty, which increases the transport cost per litre.
The only way the driver could see how much milk was in the tank, was by visual inspection. This means, when the drivers were pumping the milk across, they had to climb on top of the receiving tank to see when it was full. This practice created a trip and slip hazard for the driver and was not acceptable.
What we did:
We designed a metering system that allows the driver to interface to the flow meter via a touch screen. The driver can select the compartment number and the quantity he needs to transfer. The system starts the pump at slow speed for the first hundred litres to full the pipe with milk. After a hundred litres has been pumped through the flow meter, the system speeds up the pump. When the flow meter measures one hundred and fifty litres below the setpoint, the system slows the pump down to eliminate air bubbles in the flow meter. When the selected quantity has been transferred the pump stops.
The metering system measures the milk temperature and stops the pump if the milk is out of specification. The driver then has an option to stop the transfer or to continue the transfer after he gets confirmation from the factory.
The metering system is fitted with a printer that prints a docket after the driver has completed the transfer. The docket is handed to the factory for proof of quantity.
Outcome:
The driver no longer needs to climb on top of the tank to monitor the quantity of milk transferred, this has eliminated the associated health and safety risks.
The system stops any spillage of milk and the truck is not running half empty to the factory, so each load is optimised. The transport company can also better manage their fleet by knowing how much milk they carry on each trip.
The factory also gets a record of the amount of milk that is delivered by the transport company.
ENERGY MONITORING SYSTEM
Project: Energy monitoring software
Client: Bonson Industrial Co. Ltd
This client, based in West Auckland, has several manufacturing machines that produce food packaging containers. All the machines are installed in a single production hall. Each machine has an electrical feed from a main switch board and has its own circuit breaker. These machines are used seven days a week, twenty-four hours a day.
Problem:
Our client needed to calculate the energy cost for each machine.
· The machines were not fitted with any monitoring devices.
· The client could not measure the electricity cost to manufacture their products.
What we did:
We designed a tailor-made energy monitoring software that recorded the power usage on each individual machine in real time.
The power usage is recorded into a database installed on a central utility computer. We developed customised reporting software that retrieves data from the database and populates the power readings into a report file. This energy monitoring software populates the report file automatically after the completion of every shift.
Outcome:
The client can now calculate the energy cost for running each machine per shift and the running cost over a twenty-four-hour period. This allows production to run their lower profit margin products on more efficient machines and the client can now accurately calculate the manufacturing cost for each different product. Storing the data in a database allows for data retention, and access to historical data.